大家好,我是益至讲坛的小编,欢迎大家阅读本期益至讲坛的内容。
- 1 -
很多工厂企业在进行精益改善时,都会十分注重做好标准作业的工作。因为在大多数情况下,工厂企业都能够通过标准作业来指导生产人员按照标准化的操作动作和工作流程来完成生产任务,从而达到提高生产效率的效果。
- 2 -
虽然标准作业是能够有效的帮助生产人员提高生产效率,但是如果工厂企业过度最求通过标准作业来达到更高的生产效率提升,反而可能会让员工产生抵触心理,大大影响工作效率。
有一些工厂企业可能会出现这样的一种情况,就是在推行标准作业后,高层领导在看到生产效率有明显提升的效果后,就要求推行精益改善的负责人员,要更多的对实行动作和时间进行研究,要求他们他们测量操作者执行作业的标准时间,分秒计较,试图挤压出哪怕一点点的劳动生产率。
那么,在这样的情况下,在生产岗位上的那些坦诚地和工业工程师分享工作实务心得的员工很快发现工作的标准又更加提高了,它们的工作更加辛苦,但是最后却发现他们的工资并没有一点提高。
于是,员工学聪明了,当有人来进行现场研究时,他们就会把自己发明的技巧与省力的方法隐藏起来,放慢速度,如此一来,工厂企业的主管领导们才不会对他们拟定更高的期望。
推行精益的管理人员也发现了操作员的伎俩,于是,他们会偷偷观察操作员的工作情形。工作效率和时间研究结果往往会改变职务说明与责任,导致生产员工产生不满,最终演变为劳资冲突的主要原因。
- 3 -
在当今信息化技术高度发达的情况下,有很多工厂企业往往都会使用计算机来准确监视员工的动作,通过数据分析就能够立即知道个别员工的效率。不过,工厂员工在知道他们受到监视后,往往他们就会采取极端的方式来应对,就是只追求满足数量而不管品质。
因此在这样的状况下培育出来的员工,他们都将会变成数字的奴隶,不再重视公司的使命陈述和理念。对于产品的生产品质也无暇顾及,只是用尽全力去一次次的完成越来越高的工作要求。
这些工厂企业虽然实现了通过人力来高速生产的目的,但是最终的结果往往就是产品品质大幅下降,反而得不偿失。
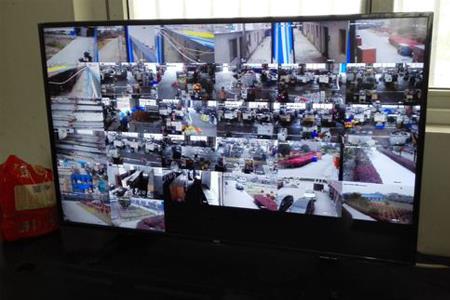
- 4 -
那么我们应该要怎样利用好标准作业来稳定提升工人生产效率呢?其实我们可以从日本的丰田公司身上找到答案。
在丰田汽车公司,制造工作的标准化概念被广泛认同,并非只是操作员工必须遵守的工作步骤。
丰田公司前社长张富士夫曾经说过:“丰田的标准化工作包含3个基本要素——生产间隔时间(以顾客要求之速度完成一项工作所需时间);执行工作的步骤程序或流程顺序;个别操作员为完成此标准化工作,手边需要的存货量。标准工作就是以生产间隔时间、步骤顺序、手边存货量这三项要素来制定的”。
丰田公司将标准化这项工作去芜存菁,原本被视为微小或没有利益的项目,在丰田模式变得更加有利、有效益的项目,同时建立了管理人员和员工共同合作的团队,而不是劳资双方的冲突。
日本的丰田公司之所以能够在运用工作标准化的过程中成功地避免了上述情形,原因就是丰田公司从未刻意的将工作标准化作为强加于员工的一项管理工具。丰田公司不会实行可能使工作变得刻板或使之降级的僵化标准,而是把工作标准化作为对员工的授权,同时变成员工持续改进的基础。
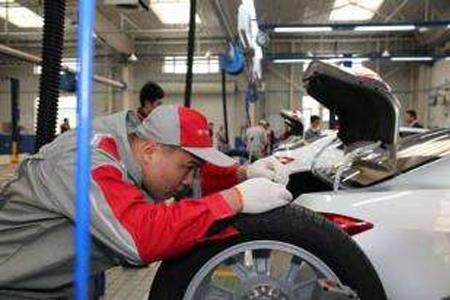
- 5 -
以上就是今天和大家分享的内容,大家对如何做好标准作业有什么看法?或者有什么工作心得?欢迎大家在下方留言,我们一起聊聊。另外,如果觉得此文让你小有收获,别忘了转发朋友圈哦~
在广州地区的企业家朋友欢迎您带着问题来参与我们每周六开展精益研讨沙龙,想参加的朋友,可以在百度直接搜索“益至咨询”就能找到我们了。
益至咨询网址:http://www.yizlean.com/