原油电脱盐基本只能对原油中存在的钠离子等进行脱除,钙、镁、铁等大部分金属以环烷酸盐、酚盐等形式存在,要将金属离子脱除,要有针对性选用脱盐剂,本文通过金陵石化公司选用的两种脱盐剂进行对比分析,总结分析了适合金陵石化公司二套常减压在炼制达混油时适合的脱盐剂型号。
原油在炼制前需进行脱盐预处理,目前原油电脱盐技术只能通过原油脱水脱除溶于水中的盐类、亲水悬浮固体和过滤性固体颗粒。原油中金属化合物除钠以氯化物等无机盐形式存在外,钙、镁、铁等大部分金属以环烷酸盐、酚盐等形式存在,只有少部分以可溶于水的无机盐形式存在,而镍、钒多以卟啉类化合物或沥青质形态存在。因此,只依靠电脱盐无法脱除原油中大部分钙、镁、铁。在原油加工过程中,金属杂质尤其是钙元素能在换热器和加热炉管的内壁沉积结垢,使换热器内介质流速降低,管壁温度升高,影响换热器传热效果,而沉积物分解还会产生碱性腐蚀,加剧换热器腐蚀;在重油加氢裂化中,钙元素容易在催化剂上结垢,并使催化剂活性迅速降低;铁化物在催化剂床层沉积,堵塞床层通道,影响加氢裂化过程的正常进行;钙、镁等元素还能导致催化裂化催化剂永久失活,铁元素能降低催化剂的选择性;钙、镁、铁等元素还是装置油垢的主要成分和延迟焦化石油焦中的灰分。原油中钙、镁、铁等金属杂质几乎影响石油加工的全过程,给生产造成重大的经济损失,因此,对原油进行脱金属处理及其重要,其经济效益非常可观。
1 脱金属剂在电脱盐工艺中脱金属原理
为了达到从原油中脱金属的目的,国内外科研人员提出了不少脱金属的方法。含磷化合物用过氧化氢、过氧酸盐预精制后,可增强从原油中脱金属的效果;用吡啶以腈、二甲基酰胺和酸抽提,可从原油中脱除部分金属杂质;用吡咯婉酮-乙醇混合物萃取其中金属杂质;用乙二酸四乙酸及其盐也能脱除原油中的金属杂质。这些方法因工艺复杂、药剂来源少,或因药剂用量大、成本高等原因,均未在工业上获得应用。
利用原油电脱盐装置在脱盐的同时,达到脱除金属杂质的目的,必须把原油中的有机金属化合物转化成能溶于水或分散到水中的物质。根据酚盐、环烷酸盐的性质,它们与水接触时,存在电离平衡,要想将金属离子从有机化合物中电离出来,从理论上讲,可以通过加强酸、沉淀剂或螯合剂等方法实现,因此,这三类物质都可以作为从原油中脱除金属杂质的脱金属剂。通过对脱金属剂的选择和复配,可生产出适合工业生产需要的脱金属剂。
脱金属剂的作用原理是,将定量的脱金属剂与破乳剂一同溶于电脱盐注水中,水与原油经混合器充分混合而分散成很小的水滴。在油水界面,溶于水的脱金属剂与原油中的有机金属化合物作用,使金属离子电离或形成沉淀物、螯合物,从而溶解或分散到水中。油水混合物在电场和破乳剂的共同作用下,小水滴迅速聚集成大水滴并从油相中分离出来,最终达到原油脱金属的目的。
2 原油电脱盐工艺介绍
金陵石化股份有限公司二套常减压电脱盐装置为两级脱盐工艺,其工艺流程见图1。
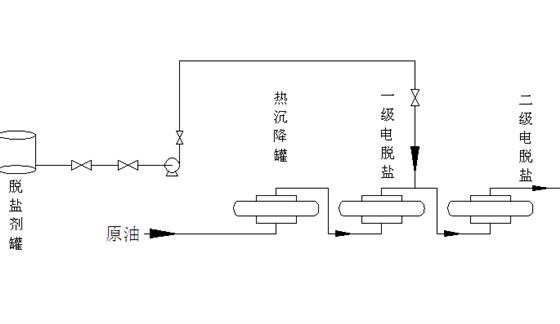
图1
该工区主要炼制高硫高酸原油,根据多年实践经验,其电脱盐装置最佳工艺条件见表1。
表1 电脱盐装置工艺条件
|
||
工艺指标
|
一级脱盐
|
二级脱盐
|
原油加工量t/d
|
9000
|
|
脱盐温度℃
|
130
|
126
|
压力/MPa
|
1.3
|
1.25
|
罐内停留时间/min
|
30
|
30
|
强电场停留时间/
|
13
|
13
|
原油在强电场上升速度/
|
120
|
120
|
强电场强度/
|
750
|
750
|
弱电场强度/
|
400
|
400
|
电耗/
|
0.3
|
0.3
|
破乳剂注入浓度/ppm
|
10
|
10
|
注水量/t/h
|
5.6
|
5.6
|
注水方式/
|
循环注水
|
|
含盐量/
|
<4
|
<2
|
含水量/
|
<0.1
|
<0.02
|
总脱盐率/
|
>96
|
|
排水含油/
|
<200
|
3 脱金属剂应用效果评价
电脱盐装置工艺条件保持不变,在注水、破乳剂等用量不变的情况下,加注脱金属剂,考察了脱金属对原油脱金属率、电流电压、含油污水的影响。由于此类脱金属剂对原油脱钙率的提高最为有效,所以通常称其为脱钙剂。
3.1 脱钙剂对原油脱金属率的影响
为筛选出适合工区使用的脱盐剂,二套常减压先后几年实验不同型号脱盐剂,其中包括NS-71、WTH-2等型号,根据原有品种、注入量等综合实验了脱盐剂在二套常减压的应用情况,较为详细的考察了电脱盐装置加注脱钙剂前后及脱钙浓度量对原油金属脱除率的影响,结果列入表2,表3,实验数据如下:
表2 NS-71对原油脱金属率的影响
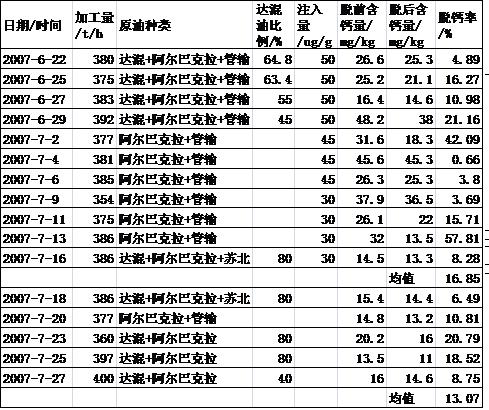
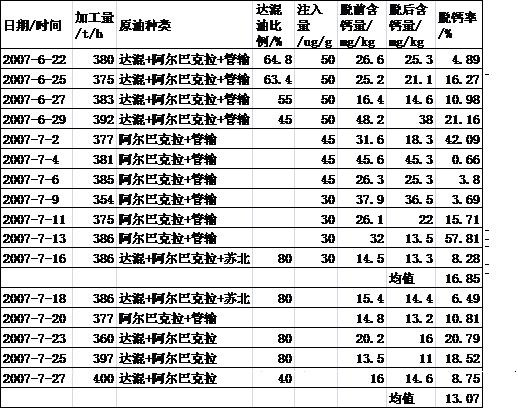
表3 WTH-2对原油脱金属率的影响
从上表数据看出,加注脱钙剂可显著提高原油中金属离子的脱除率,其中针对钙离子的脱除效果最为明显。增加脱钙剂的浓度可提高原油中的金属脱除率,当WTH-02型脱钙剂浓度为90mg/L时,脱钙率由41%提高到80%左右。加注脱钙剂对试验阶段脱盐率没有任何不利影响,而且根据相对试验数据统计,其对原油脱盐有较好的协同效应,可略微提高脱盐效果。
3.2 脱钙剂对电脱盐装置电流、电压的影响
电脱盐装置中加入脱钙剂后,考察了脱钙剂对两级脱盐工艺中电压和电流的影响,结果列入表3。
表4 脱钙剂对电脱盐装置电压、电流的影响
|
||||
脱钙剂
|
一级 电压/V
|
一级 电流/A
|
二级 电压/V
|
二级 电流/A
|
空白
|
380
|
190
|
350
|
170
|
NS-71型
|
400
|
130
|
380
|
140
|
WTH-2型
|
410
|
56
|
390
|
62
|
从表4数据可见,电脱盐装置注入脱钙剂后,电流缓缓下降,电压则缓慢上升,最终电流下降50%左右,电压上升20%左右,有利于电脱盐装置的平稳操作,同时也有明显的节能效果。
3.3 脱钙剂对含油污水的影响
加注NS-71型脱钙剂后,含油污水乳化现象严重,不利于絮凝,含油污水不合格率相对较高,增加了环保成本。WTH-2型脱钙剂的注入,对含油污水处理成本影响不大。
3.4 脱钙剂使用过程中注意事项
NS-71型脱钙剂在使用配制过程中有溶解困难的问题。WHT-02型脱钙剂在冬季气温较低时,有效成分无结晶,属于水溶性,配置方便,但属于强酸类,对配制罐等设备腐蚀较为严重,二套常减压原注入点因阀门腐蚀,注入阀门无法修复,后改为二次注水线注入。
从工艺操作情况看,在加工达混油时注入WTH-02脱盐剂,操作相对平稳,没有因为脱盐剂的注入出现波动,脱盐罐压力控制平稳,脱盐排水清白,含油量平均在105㎎/L,远低于环保指标300㎎/L,从原油脱前拖后钙含量分析,该脱盐剂在装置加工达混油时脱盐效果显著。
4 脱金属剂工业应用前景
脱金属剂在我国已有10年左右的开发历程,并在天津、武汉、齐鲁、扬子、兰州等一批炼油厂进行了适用性试验,但尚未工业普及,其中有多方面的因素。从工业试验结果看,各种脱金属剂对原油脱金属率提高确有显著效果,但由于装置局限性以及原油炼制成本增加等限制,目前未得到关于减轻腐蚀和催化剂中毒的量化数据。
但是原油脱金属作为一项新技术有着广阔的应用前景,在今后的生产应用中,一方面要进一步研究并量化其对提高油品质量、减轻腐蚀、减少催化剂中毒等作用,另一方面大力降低脱钙剂生产成本,使脱钙剂使用更加方便可靠,从而促进电脱盐技术迈上新台阶,为炼油厂取得更大经济效益做出贡献。